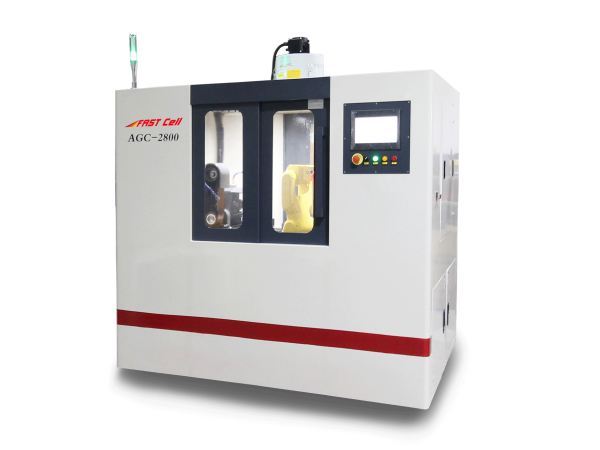
Automatic Grinding Center AGC-2800
AGC-2800 was developed and manufactured based upon our strong R&D capabilities and years of experience in the automation industry. AGC-2800 with built-in 6-axis Robot is a multi-function grinding machine that excels in rough grinding, fine grinding, finishing grinding and chamfering.
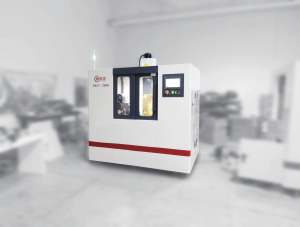
Fully enclosed guard and transparent design
Fully enclosed guard providing safety and environmental protection; Anti-explosion glass allowing full visualisation of the machine operation.
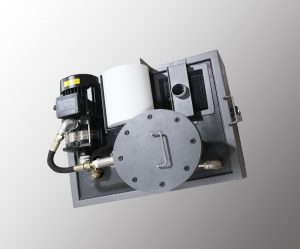
Oil Filtration System
Ensure the quality of the recycled oil during the spraying process to prolong the life cycle of the abrasive paper, and increase the surface finish of the workpiece.
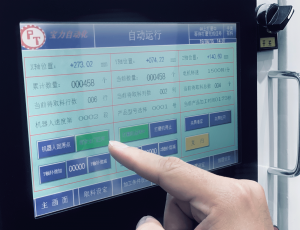
Pro-technic SMART operation system
Exclusively developed to reduce setup time, quick start design and automatied material changing system; predictive maintenance function and malfunction diagnostic function.
Flexible abrasive belt and disc combination module
Specially selected servo motor reducing and vibration;Continuously variable transmission prolongingthe life cycle of the abrasive paper; Fulfill various grinding requirements
Structure of Abrasive Discs
Duo-discs design allowing flexbility between rough grinding and fine grinding; X-axis movement ensures grinding quality and consistency;Y-axis movement increases grinding accuracy
Innovated Software — Refined Grinding Technique
Utilising offline CAD/CAM softwares to simulate robot movements, automatically generating programs to reduce set up time as well as performing grinding duties not achievable manually.
Advantages of AGC-2800 VS Disadvantage of manual grinding
Advantages of AGC-2800 | Disadvantage of manual grinding |
One operator can manage several AGCs, increasing productivity and reducing cost | One operator can only manage single process |
High positioning accuracy and controlled torque allowing consistent, good finishing | Inconsistent grinding quality and surface finish |
Continuous spraying of coolant allowing stable surface structure | Workpiece will heat up during manual grinding, affecting the surface structure |
Reducing occupational hazards associated with manual grinding processes | Occupational hazards from dust, oil mist and noise pollutions |
Fully enclosed guard with oil mist collector ensuring safe working place environment | Traditional grinding stations may cause dust explosion |
Operating expenses under control with no labour shortage problem | Labour cost inflation and have labour shortage problem |
Multi-station, Multi-task reducing fixture set up time | The need to set up fixture for multi-positions,grinding will affect accuracy, reposition will cause accuracy deviation |
Swing motion of the servo motor to enlarge the grinding area | Grinding area is fixed, particular area cannot be grinded |
Application
![]() |
Product: | Watch case |
Material: | Stainless Steel | |
Method: | 6-Axis Robot | |
Positions: | Body, face, bevel | |
Duration: | ~120s |
Procedure: | 1. No. 1 Abrasive Disc – Rough grinding by #600 abrasive paper |
2. No. 2 Abrasive Disc – Fine grinding by #1200 abrasive paper | |
3. No. 3 Abrasive Disc Finishing grinding by #1500/#2000 abrasive paper |
Standard Accessories
Structure | Structure Dimension: 1,960(L) * 1,475(W) * 2,330(H) (mm) Weight: ~ 1,900 kg | 1 set |
Robot | Brand: Fanuc Mate 200iD Controller: R-30IB Mate I/O Port: CCLink Arm Length / Loading : Radius 717mm; 7kg Repeatability/Safety Level +/-0.02mm;IP67 | 1 set |
Grinding unit | 3 sets Abrasive Disc (Select) Max. Rotating speed: 2,800rpm (Adjustable) Spindle power: 1.5kW Tray: φ210mm Max. dimension of the abrasive disc: φ210mm Min. dimension of the abrasive disc: φ80mm | 1 set |
1set Abrasive belt (Select) Max. rotating speed: 2,800rpm (Adjustable) Spindle power: 0.75kW Length of the abrasive belt: 914mm Max. width: 100mm, Min. width: 50mm 1 set | ||
Spraying system | 60L oil tank with filtering device, cooling oil spraying the grinding area custom-made | 1 set |
Slideway | Abrasive disc device and abrasive belt device installed on the slideway, Max. speed 15m/min (Adjustable) | 1 set |
Electrical control system | Mitsubishi PLC, Mitsubishi Touch panel and custom-made operational software | 1 set |
Optional Accessories
Oil Mist Collector | Power 0.55kW flow rate 425 m³/h | 1 set |
CCD positioning system | With cam, light, controller, cable and bracket | 1 set |
Repositioning device | With take-off material inspection | 1 set |
utomatic Side door | With safety sensor | 1 set |
Clamping device of robot | Cylinder control, not including sample workpiece | 1 set |
Workpiece clamping | Custom-made | 1 set |
Offline programming software | Mastercam Robotmaster | 1 set |
Tray positioning device | Positioning by frame Max. dimension of loading tray: 300*250mm Max. dimension of unloading tray: 330*230mm Install each loading and unloading tray at the same time | 1 set |